Di-Dro Advanced Hydraulic Delay System
Di-Dro is a Hydraulic Tool and Die Delay System comprised of hydraulic springs that are mounted to a base and controlled via adjustable valves and an accumulator. Similar in function to self-contained delay springs, the Di-Dro delay system solves issues that can occur using standard gas springs – such as part reversal, press wear from reverse tonnage, and mistiming of part ejection.
Di-Dro's components are made from high-quality materials that ensure longevity, and is engineered for seamless integration with existing systems, making it a versatile choice for various applications.
- Easy to use for multiple tools
- Only requires a small footprint
- Designed to a maximum of 4000 psi
- Can be used in an upper and lower application
- Provides constant force throughout the stroke
- Pad delay can be activated with an electric or pneumatic signal
- Bore Seal Cylinders withstand contamination in various applications
Plated Hydraulic Delay System | Modular Hydraulic Delay System |
![]() |
![]() |
Why Use Hydraulic Delay Systems Vs Self-Contained Delay Springs?
The Di-Dro Hydraulic Delay System brings significant performance advantages over delay springs, while being 2, 3, or 4 times less expensive than a servo press.
- Faster
- Handles Heat Better
- Adjustable Stroke Length
- Longer Run Times
- Heavier Tonnage
- Automation timing
How it Works
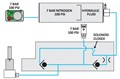
1. Cycle begins with system at low pressure (7bar/100 psi) and solenoid closed.
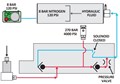
2. When the cylinder is compressed, the pressure valve creates forming force. Fluid from the cylinder moves to the accumulator. High pressure occurs only when the cylinder is being compressed.
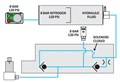
3. Cylinder is delayed in the retracted position as long as the solenoid is closed.
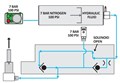
4. The Solenoid opens and nitrogen pressure in the accumulator pushes fluid back to the cylinder which returns to the raised position. The system is reset and ready for the next cycle.
How to Get Started
You don’t need to be an expert. Hyson’s team of engineers is able to partner with you to develop a solution that meets your needs. To get the conversation rolling, it would be helpful for you to have some information:
- Number of pressure points
- Total force required (N)
- Cylinder work stroke (mm)
- Desired parts per minute (ppm)
- Maximum ram speed during work stroke (m/s)
Or
- Mechanical press stroke length (mm)
- Maximum anticipated press speed in strokes per minute (spm)